وبلاگ
پوشش های پایه آب، پلیمری،امولیسونی
پوشش های پایه آب، پلیمری،امولیسونی
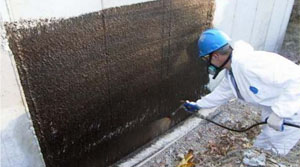
آنچه می خوانید :
پوشش های پایه آب
مقدمه
بسیاری از پوشش های پایه حلال مدرن بسیار مهم، اپوکسی ها، آلکیدها و اکریلیک ها، در فرمولاسیون های پایه آب نیز در دسترس می باشند. در سال های اخیر، حتی تکنولوژی های پلیمرهای یورتانی در پوشش های پایه آب مورد استفاده قرار گرفته اند. رنگ های پایه آب،رنگ های پایه حلالی نمی باشند که به آسانی حلال آلی در آن با آب جایگزین شود، بنابراین شیمیست های رنگی باید یک فرمولاسیون کلی جدید برای سیستم مورد نظر طراحی نمایند. در این مقاله بررسی میکنیم که رنگ های پایه آب چگونه از رنگ های پایه حلال متفاوت می باشند.
این مرحله هنگامی آغاز می شود که تنها باقی مانده بین ذرات باشد. در دومین مرحله، که مرحله مویینگی هم نامیده می شود، کشش سطحی بالای آب یک فاکتور می شود. آب تلاش می کند تا کشش سطحی خود در فصل مشترک آب-هوا و آب-ذرات را کاهش دهد. در واقع آب باعث تغییر شکل ذرات پلیمری جامد می شود. این اتفاق در بالا، پایین و دو طرف کره و هر جایی که با کره دیگر در تماس است، رخ می دهد. و نتیجه آن ایجاد ساختار لانه زنبوری دودکاهدرال می باشد.
نفوذ ماکروملکولی
تحت شرایط ویژه، مانند دمای به اندازه کافی بالا، زنجیرهای پلیمری می توانند درون مرزهای ذرات نفوذ کنند و یک فیلم پیوسته و همگن شکل می گیرد. استحکام مکانیکی و مقاومت آبی فیلم افزایش می یابد.
نیروی محرکه تشکیل فیلم
فرآیند تشکیل فیلم بسیار پیچیده است. تعداد زیادی تئوری های مختلف برای توصیف این فرآیند وجود دارد. تفاوت عمده ی آنها در نیروی محرکه برای تغییر شکل ذرات: کشش سطحی ذرات پلیمر، جاذبه ی واندروالسی، کشش بین سطحی پلیمر-آب، فشار مویینگی در فصل مشترک آب-هوا یا ترکیبی از این ها می باشد.
این تئوری های مکانیزم تشکیل فیلم لاتکس، برای بهبود رنگ های پایه آب و طراحی نسل های بعدی این رنگ ها ضروری و لازم است. برای بهبود سرعت تشکیل فیلم، اگر نیروی محرکه اصلی برای انعقاد در فصل مشترک بین پلیمر و آب، بین آب و هوا، یا بین ذرات پلیمر قرار گرفته است، دانستن اینکه این موقعیت تعیین می نماید که چه کشش سطحی یا انرژی سطحی باید بهینه شود، بسیار اهمیت دارد.
در سالهای اخیر، به این اتفاق نظر رسیده اند که کشش سطحی آب، چه در فصل مشترک هوا-آب مشترک پلیمر-آب یا هر دو، نیروی محرکه است. مطالعات AFM نشان می دهد که فشار مویینگی در فصل مشترک هوا-آب از اهمیت بسیار بیشتری برخوردار است. Visscher و همکارانش تحقیقات طبق روش دیگری، نتایج یکسانی را گزارش نموده اند. آنها هنگام تغییر شکل پلیمر برای یک سیستم نیروهای مختلفی را تخمین زده اند که برای تغییر شکل ذرات نیروی 107 نیوتونی مورد نیاز است. نیروهای ایجاد شده توسط مویینگی آب بین ذرات و توسط فصل مشترک آب-هوا هر دو به اندازه کافی بزرگ هستند.
تقریب نیروهای ایجاد شده در طول تغییر شکل ذرات
مقدار تقریبی (نیوتون) | نوع عامل نیرو |
6.4 × 10-17 | نیروی جاذبه بر روی ذرات |
8.4 × 10-12 | نیروهای واندروالسی در فاصله ۵ نانومتری |
5.5 x 10-9 | نیروهای واندروالسی در فاصله ۰،۲ نانومتری |
2.8 × 10-10 | دافعه الکترواستاتیک |
2.6 × 10-7 | نیروی مویینگی به دلیل فصل مشترک آب-هوا |
1.1 × 10-7 | نیروی مویینگی به دلیل پل های مایع |
Gauthier و همکارانش اشاره کرده اند که کشش بین سطحی پلیمر-آب و فشار مویینگی در فصل مشترک آب-هوا بیان کننده ی پدیده ی فیزیکی مشابهی می باشند و توسط قانون یانگ و لاپلاس برای انرژی سطحی قابل توصیف می باشند. در حقیقت دو حداقل دمای تشکیل فیلم وجود دارد، یکی تر و دیگری خشک. که ممکن است نشان دهنده ی این باشد که فصل مشترک آب-پلیمر و تبخیر آب بینابینی، محرکه ی تشکیل فیلم می باشند.
رطوبت و پخت لاتکس
بر خلاف حلال های آلی، آب به مقدار زیادی در اتمسفر موجود می باشد. محققان تخمین زده اند که اتمسفر حاوی 1015*6 لیتر آب می باشد. به همین دلیل، رطوبت نسبی بر روی سرعت تبخیر آب در رنگ های پایه آب تاثیر می گذارد. مقالات تجاری نشان می دهند که پوشش های پایه آب به رطوبت بالا حساس می باشند. گرچه محققانی مانند .Laven, Visschers و Vander linde به خوبی نشان داده اند که این عقیده اشتباه است. آنها از ترکیبی از تئوری های ترمودینامیکی و زاویه تماس برای اثبات اینکه رنگ های لاتکس عملا در تمام رطوبت ها در مدت زمانی که آنها مستقیما توسط بارندگی یا کندانسیون تر نشده اند، خشک می شوند. این نتایج از آزمایشات Forsgren و Palmgren نیز دیده شده است که آنها یافتند که تغییرات در رطوبت نسبی اثر چشمگیری در خواص مکانیکی و فیزیکی پوشش پخت شده ندارد Gauthier و همکارانش به طور تجربی نشان دادند که انعقاد لاتکس به رطوبت محیط بستگی ندارد در مطالعات تبخیر آب با استفاده از اندازه گیری کاهش وزن آنها یافتند که در یک دمای مشخص سرعت در مرحله یک به رطوبت محیط وابسته است. در
مرحله 2 از آنجا که انعقاد رخ می دهد، سرعت تبخیر آب را نمی توان توسط مدل مشابه توصیف نمود.
پوشش های واقعی
مدل های تشکیل فیلم توصیف شده در بالا، برای سیستم های برپایه ی لاتکس تنهاست. پوشش های لاتکس پایه آب واقعی حاوی اجزای بیشتری است، مانند انواع مختلف پیگمنت، عامل انعقاد کننده برای نرم کردن بخش بیرونی ذرات پلیمری، سورفکتانت و امولسیفایر و غلظت دهنده برای کنترل ترکنندگی، ویسکوزیته و تثبیت دیسپرژن.
موفقیت رنگ پایه آب در تشکیل یک فیلم پیوسته وابسته به تعدادی از فاکتورهاست که در زیر آورده شده است:
- ترشوندگی ذرات پلیمری توسط آب (Visschers و همکارانش دریافتند که زاویه تماس آب برروی سطح ذرات پلیمری تاثیر چشمگیری در نیروی تماسی که ذرات پلیمری را از هم جدا (در صورت مثبت بودن) و یا به هم نزدیک می نماید (در صورت منفی بودن) دارد).
- سختی پلیمر
- میزان موثر بودن عامل انعقاد کننده
- نسبت بایندر به پیگمنت
- دیسپرژن ذرات پلیمری درون ذرات پیگمنت
- اندازه نسبی پیگمنت به بایندر در لاتکس
پیگمنت
در فرمولاسیون یک رنگ، چه پایه حلال و چه پایه آب، پیگمنت باید به خوبی دیسپرس شود، هنگام پخت توسط بایندر پوشش داده شود و در نسبت مناسبی با بایندر ترکیب شود. نکته آخر در مورد سیستم های پایه حلال و پایه آب مشابه است، در حالیکه که دو مورد اولی در پوشش های پایه آب باید مورد توجه قرار گیرد.
کشش سطحی بالای آب نه تنها دیسپرژن پلیمر را تحت تاثیر قرار می دهد بلکه دیسپرژن پیگمنت را نیز تحت تاثیر قرار می دهد. همانطور که Kobayashi اشاره نموده است، مهم ترین فاکتور در دیسپرژن پیگمنت، توانایی حلال برای تر نمودن آن است. با توجه به کشش سطحی، ترشوندگی وابسته به دو عامل است؛ آبگریزی (یا آبدوستی) و هندسه پیگمنت.
Joanicot و همکارانش آزمایش نموده اند که هنگامی که ذرات پیگمنت افزوده شده به سیستم اندازه بسیار بزرگتری از ذرات لاتکس داشته باشند، در فرآیند تشکیل فیلم چه اتفاقی رخ می دهد. آن ها دریافتند که در این مورد سیستم های پایه آب مشابه سیستم های پایه حلال رفتار می کنند، غلظت حجمی پیگمنت بحرانی است.
در پوشش های با PVC کم، فرآیند تشکیل فیلم، توسط حضور پیگمنت تحت تاثیر قرار نمی گیرد. در PVC بالا، ذرات لاتکس هنگام تبخیر آب تغییر شکل می دهند اما به مقدار کافی برای گسترش کامل در ذرات پیگمنت وجود ندارد. پوشش خشک شده شبیه ماتریسی از ذرات پیگمنت است که در بسیاری نقاط توسط ذرات لاتکس کنارهم قرار گرفته اند.
مشکلات عدم تعادل دیسپرژن پیگمنت-pvc در شکل زیر نشان داده شده است. در بخش بالایی تصویر، PVC بسیار بالاست و ذرات بایندر در برخی سایت ها بین ذرات پیگمنت، تجمع یافته اند. هنگامی که آنها تغییرشکل می دهند، فیلم حاوی ذرات پیگمنتی است که توسط پلیمر و حفره های هوا کنارهم قرار دارند. بخش میانی تصویر، نیز PVC بسیار بالایی دارد، اما در اینجا ذرات بایندر دیسپرس شده اند. ذرات پیگمنت ممکن است یک فیلم پیوسته اطراف ذرات پیگمنت تشکیل دهد اما حفره ی هوا نیز ممکن است به دلیل ناکافی بودن بایندر ایجاد شود.
قسمت بالایی تصویر، PVC کمتر است و بایندر نه تنها ذرات پیگمنت را می پوشاند بلکه هیچ حفره ای ایجاد نمی نماید و این ایده آل ترین حالت است.
افزودنی ها
در رنگ های پایه آب فرآیند تشکیل فیلم ممکن است روی لایه ی غیرهمگن رنگ پخت شده تاثیر گذارد. Tzitzinou و همکارانش، نشان داده اند که ترکیب لایه ی رنگ پخت شده انتظار می رود در راستای عمق فیلم تغییر کند. آن ها یک سورفکتانت آنیونی در یک فیلم لاتکس آکریلیک را مطالعه نمودند. با استفاده از AFM و طیف سنجی Rutherford backscattering بر روی فیلم پخت شده، آنها دریافتند که غلظت سورفکتانت در سطح بیشتر از بالک پوشش است. Wegmann نیز ناهمگنی فیلم های پایه آب را بعد از پخت مورد مطالعه قرار داد اما یافته های او عمدتا مربوط به انعقاد ناکافی در طول فرآیند پخت می باشد.
شیمی تشکیل لاتکس بسیار پیچیده است، و مدل سازی پیش بینی شده را به چالش میکشد. مشکل گزارش شده برای مدلسازان پایه آب، این است که افزایش در دمای پخت می تواند اجزای پوشش را تحت تاثیر قرار دهد. Snuparek و همکارانش یک امولسیفایر غیریونی به دیسپرژن کوپلیمر بوتیل متا أکریلات/بوتیل اکریلات/آکریلیک اسید اضافه نمودند. هنگامی که پخت در دمای 60 درجه سانتیگراد رخ می دهد، مقاومت آبی فیلم ها با مقدار امولسیفایر افزوده شده، کاهش می یابد.
حداقل دمای تشکیل فیلم
حداقل دمای تشکیل فیلم حداقل دمای مورد نیاز برای یک بایندر برای تشکیل فیلم منسجم می باشد. این اندازه گیری ها بر اساس دمای انتقال شیشه ای پلیمر می باشد. اگر یک پوشش در زیر MFFT اعمال شود، آب همانگونه که برای مرحله ۱ توصیف شد، تبخیر می شود. به دلیل اینکه که دمای محیط کمتر از MFFT می باشد، ذرات به سختی تغییر شکل می دهند. ذرات در مرحله دوم هنگام تبخیر آب باهم ادغام نمی شوند. یک ساختار لانه زنبوری با پیوندهای واندروالسی بین ذرات و نفوذ ملکول های پلیمر درون مرز ذرات، رخ نمی دهد.
MFFT را می توان در آزمایشگاه به عنوان دمای حداقل که در آن فیلم لاتکس شفاف می شود، اندازه گیری نمود. این روش بسیار آسان است زیرا اگر پوشش فیلم منسجمی تشکیل ندهد، حاوی حفره های هوا می شود. این حفره ها سطح های داخلی درون فیلم ایجاد می کنند که منجر به کدری و پشت پوشی فیلم می گردد.
لاتکس ها باید همیشه در دمای بالای NFFT اعمال شوند، که بسیار سخت تر از چیزی است که به نظر می رسد، زیرا MFFT یک مقدار دینامیکی است که با زمان تغییر می کند. در سیستم های دو جزئی ،MFFT به محض اختلاط مواد، افزایش می یابد. رنگ های پایه آب دو جزئی باید قبل از افزایش MFFT تا رسیدن به دمای اتاق، اعمال و خشک شوند. زمانیکه MFFT به دمای اتاق برسد و POT LIFE یک رنگ پایه آب به پایان برسد، ویسکوزینه افزایش نمی یابد.
MFFT خشک و MFFT تر
اگر یک رنگ لاتکس در زیر MFFT خشک شود، هیچ تغییر شکل ذره ای رخ نمی دهد. گرچه اگر دمای لاتکس خشک شده بعدا به بالای MFFT برسد، انعقاد رخ نمی دهد، برای ایجاد نیروی مویینگی هیچ سطح مشترک آب-هوا موجود نمی باشد و بنابراین تغییر شکل ذره رخ نمی دهد. اگر افزایش دما زیاد باشد، تغییر شکل ذرات رخ می دهد. به این دلیل است که، آب باقی مانده بین ذرات به دلیل تراکم مویینگی از آنجا خارج می شود. در دمای بالاتر این پل های مایع بین ذرات می تواند نیروی کافی برای تغییر شکل ذرات را ایجاد نماید.
دو NFFT وجود دارد: MFFT خشک و MFFT تر. MFFT نرمال یا تر، دمایی است که تحت شرایط عادی دیده می شود، که در آن یک لاتکس در دمای محیط و بالای دمای انتقال شیشه ای پلیمر اعمال می شود و تشکیل فیلم طبق سه مرحله ذکر شده، رخ می دهد. این MFFT مرتبط با تغییر شکل ذرات به دلیل فصل مشترک هوا – آب است.
دمای بالاتری که ذرات لاتکس غیر ادغام شده، تغییر شکل میدهند، MFFT خشک نامیده می شود. این پدیده مربوط به مقدار بسیار کمتر آب بین ذرات می باشد نقش آب در اینجا به خوبی قابل فهم نمی باشد. ممکن است که مقدار کمتر قادر به تغییر شکل ذرات باشد زیرا یک احتمال رخ دادن یک مکانیزم تغییر شکل متفاوت در دمای بالا وجود دارد. یا ممکن است تحت این شرایط ذرات پلیمری نرم تر شوند.
flash rusting
flash rusting ,Nicholson را اینگونه تعریف می نماید: خوردگی سریع زیرآیند در طول خشک شدن پوشش آبی، با ظهور محصولات خوردگی بر روی سطح فیلم خشک. flash rusting به عنوان یک مشکل احتمالی در پوشش های پایه آب معرفی می شود. اما Nicholson اشاره کرده است که این پدیده هنوز به خوبی درک نشده است و اهمیت دراز مدت آن برای پوشش ناشناخته است. مطالعات زیادی برای شناسایی افزودنی های Anti flash rusting انجام گرفته است.
بحث کلی flash rusting ممکن است غیر ضروری باشد. lgetoft اشاره نموده است که flash rusting تنها به آب نیاز ندارد بلکه به حضور نمک هم نیاز دارد.
Forsgren و Persson نتایجی بدست آوردند که نشان می دهد که در رنگ های پایه آب مدرن مشکل flash rusting یک مشکل جدی نیست. آنها از اندازه گیری زاویه تماس، FTIR و AFM برای مطالعه تغییرات شیمی سطح در سطح مشترک پوشش آکریلیک پایه آب-فولاد قبل از انجام پخت، استفاده کردند. به طور ویژه، انرژی سطحی کلی فولاد و اجزای الکترومغناطیس و اسید-باز آن، قبل و بلافاصه بعد اعمال پوشش مورد مطالعه قرار گرفتند.
انتظار میرفت که اجزای اسیدی و بازی انرژی سطحی فولاد باید بلافاصله بعد از اعمال پوشش افزایش یابند. در حالیکه که انرژی سطحی کلی کاهش می یابد و اجزای باز لوویس افت می کنند.
اندازه گیری زاویه تماس بعد از تماس با پوشش بیشتر برای پلیمرهای رایج است تا فولاد. مطالعات طیف سنجی دو دقیقه بعد از قرارگیری در معرض رنگ، گروه های کربوکسیل و آلکان را بر روی سطح فولاد نشان می دهد. میکروسکوپ نیروی اتمی نشان می دهد که بعد از مدت کوتاهی قرارگیری در معرض رنگ بر روی سطح ذرات گِرد نرمتر از فولاد وجود دارد.
نویسندگان براین باورند که تقویت کننده چسبندگی در زنجیرهای پلیمری بسیار بعد از ۲۰ ثانیه در ابتدا ذرات پلیمر به سطح فولاد متصل می شوند. اثرات این پیوندهای سریع و حفاظت از خوردگی بلندمدت شناخته شده نمی باشد. دانش بهتر فرآیند در فصل مشترک فلز-پوشش بلافاصله بعد از اعمال پوشش رخ می دهد که ممکن است به درک و جلوگیری از پدیده های نامطلوب مانند Flash Rusting کمک نماید.